白根電機なら気軽に相談できる樹脂溶接・曲げ
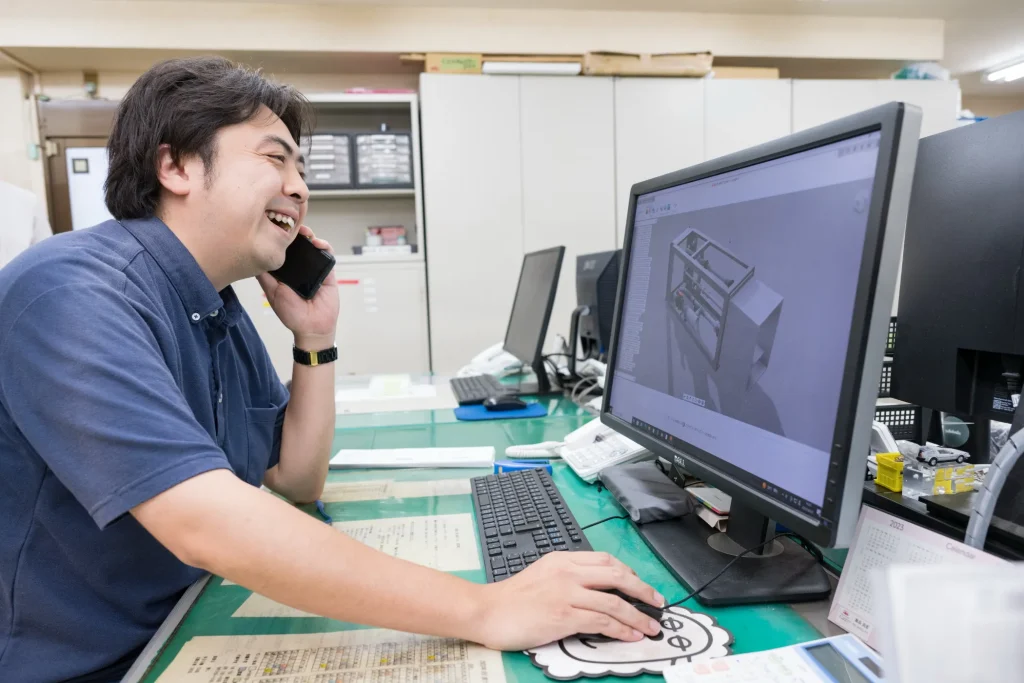
樹脂切削はできるけれど、溶接や曲げは対応不可と断られたことはありませんか?
白根電機なら切削だけでなく、溶接や曲げ、印刷や組み立てまでトータルで対応します。
例えば、大学・研究機関・医療機関・病院等の研究・実験に必要な器具やケースをオーダーメイドで製作が可能です。図面無し段階からのご要望に直接の打ち合わせにて対応が可能です。
対応材質例
ABS(原色)・ABS(黒)・耐熱塩ビ・硬質塩ビ・透明塩ビ・PMMA・PP・PE・PFA・PVDF
様々な樹脂材の溶接に実績があります。異種材の溶接も検討可能ですので、お気軽にご相談ください。
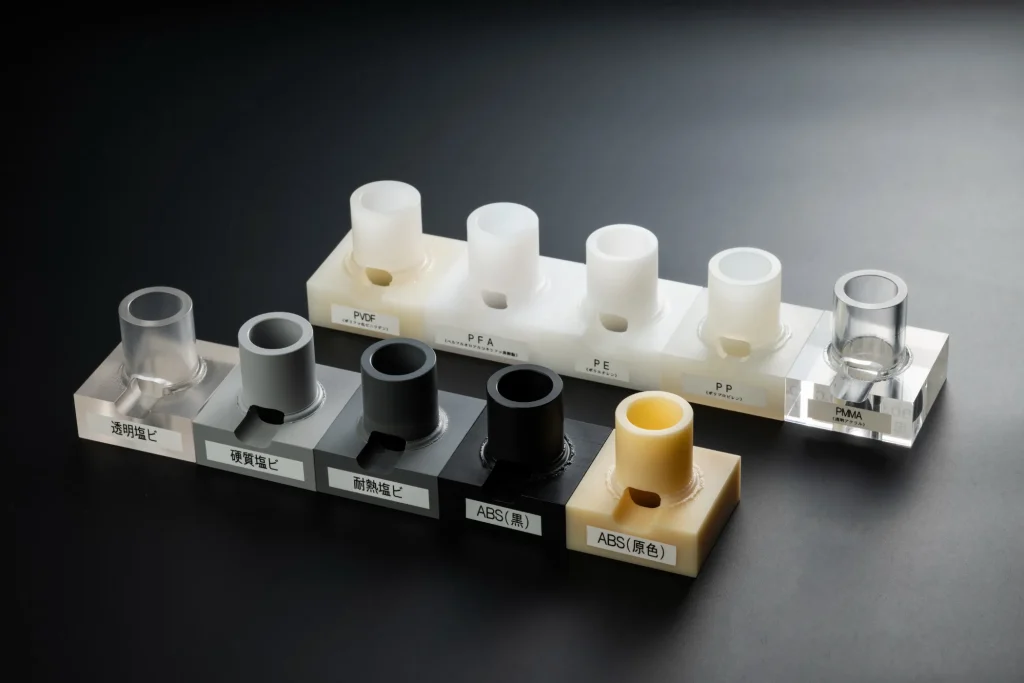
樹脂溶接の加工事例
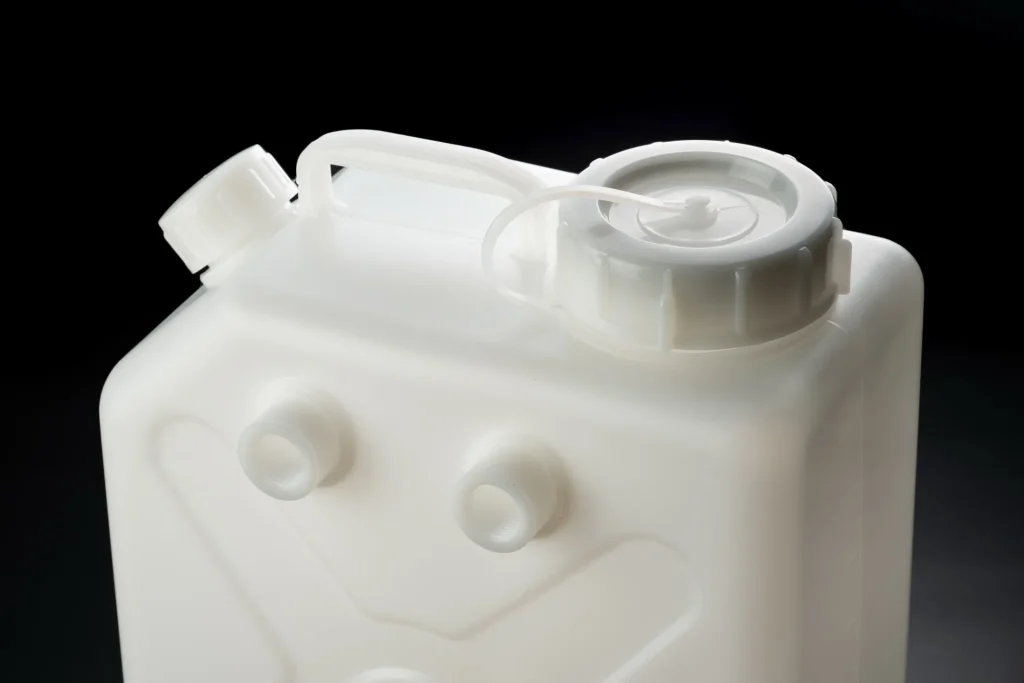
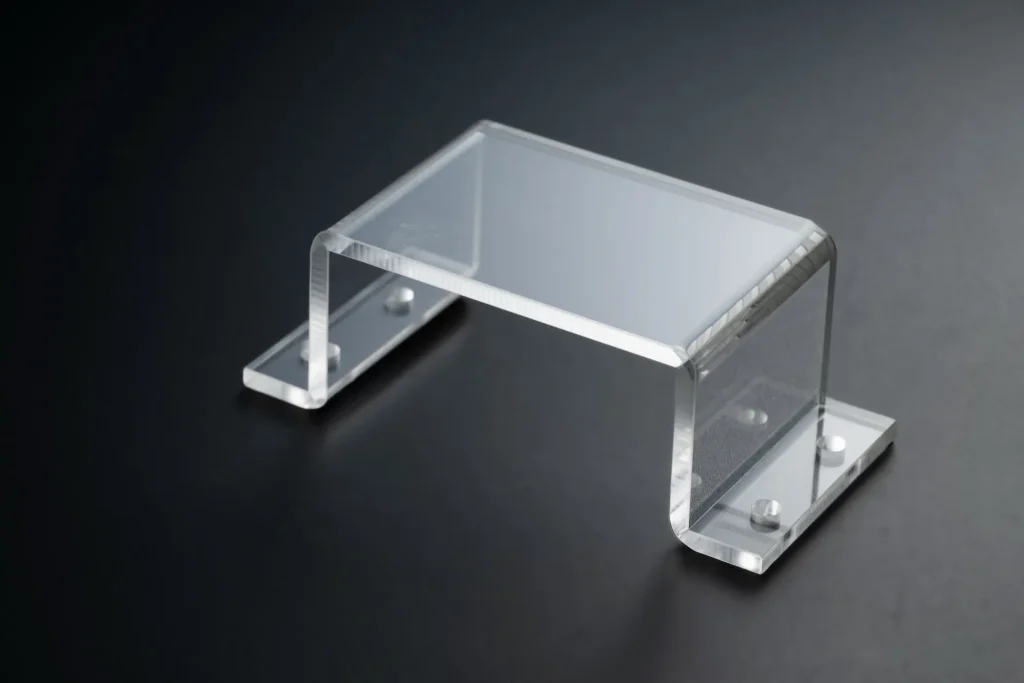
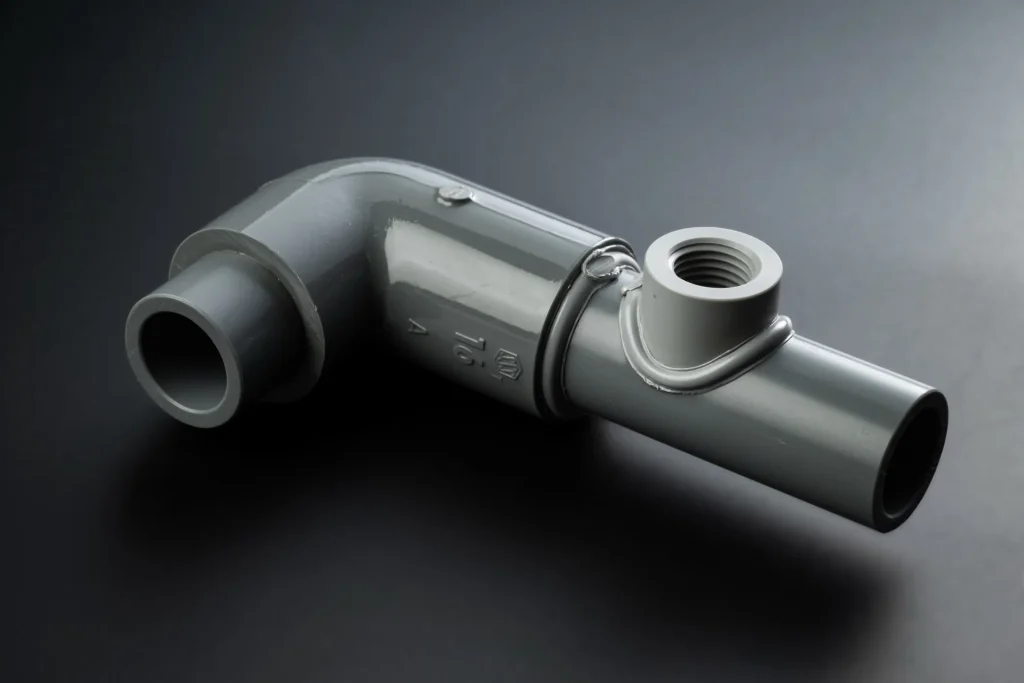
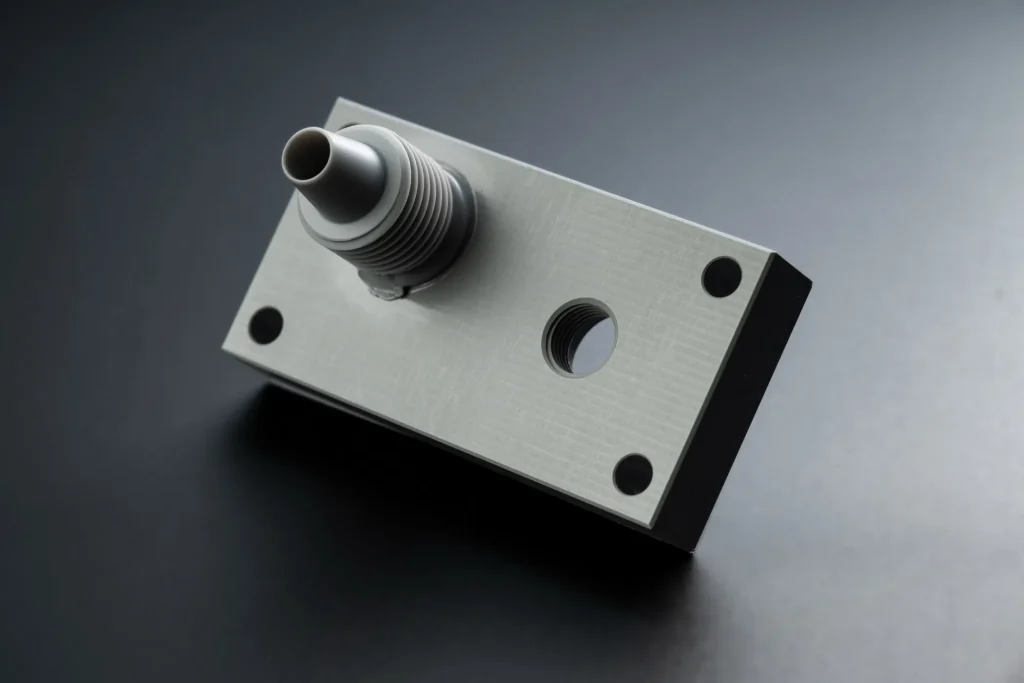
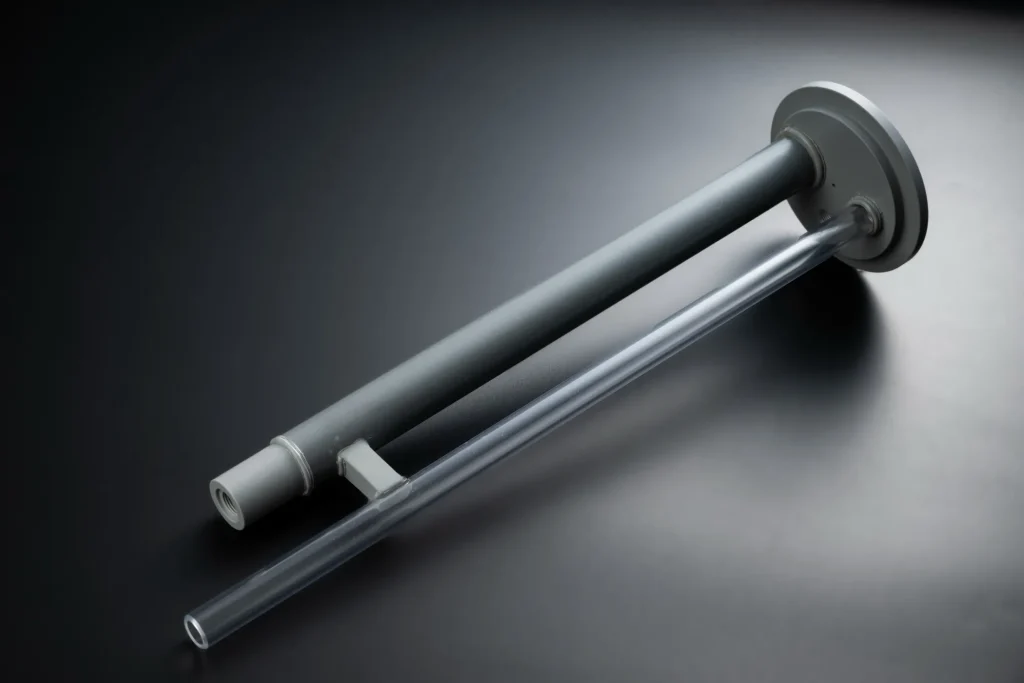
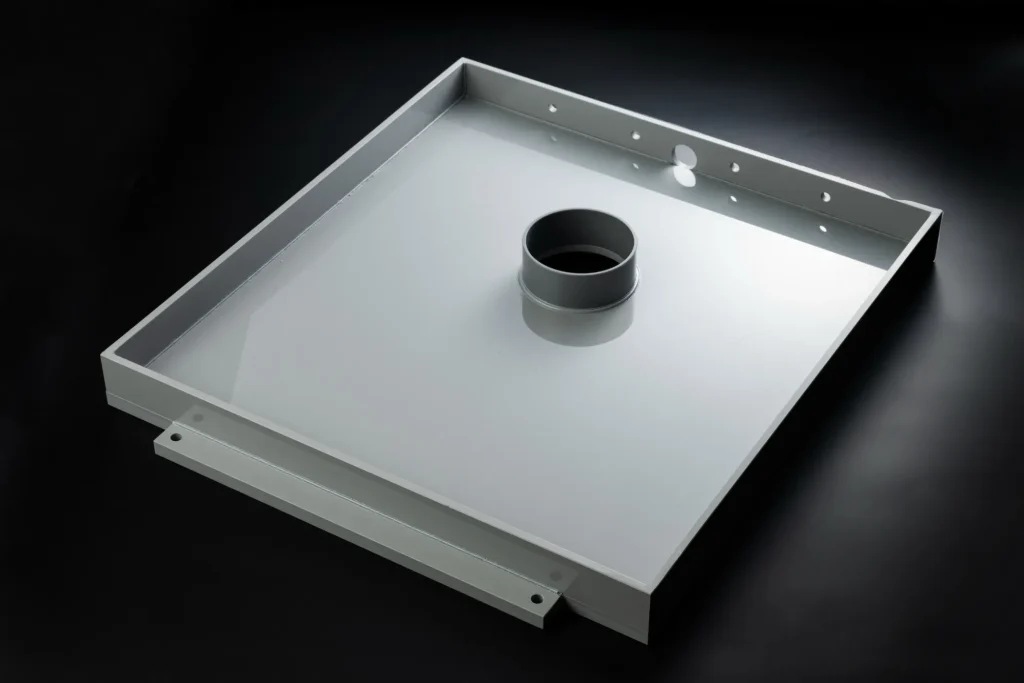
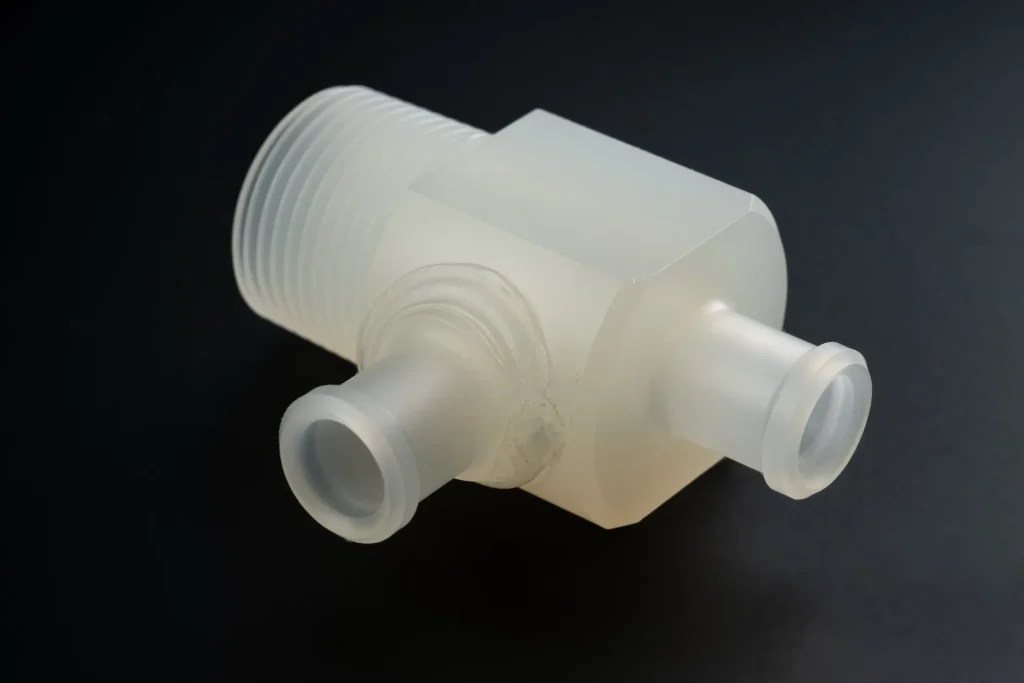
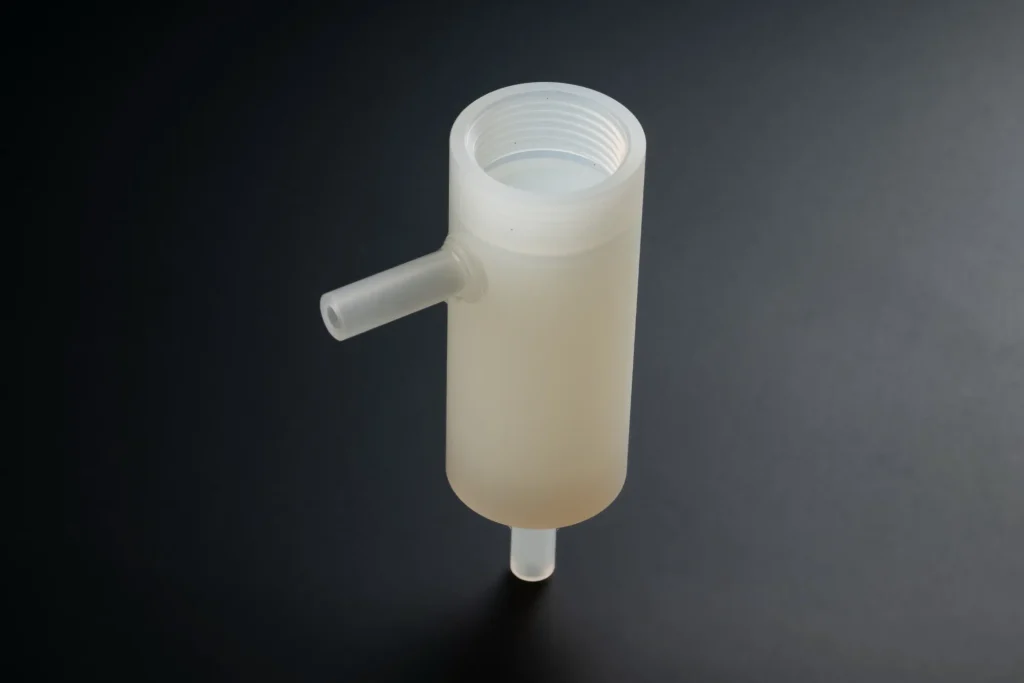
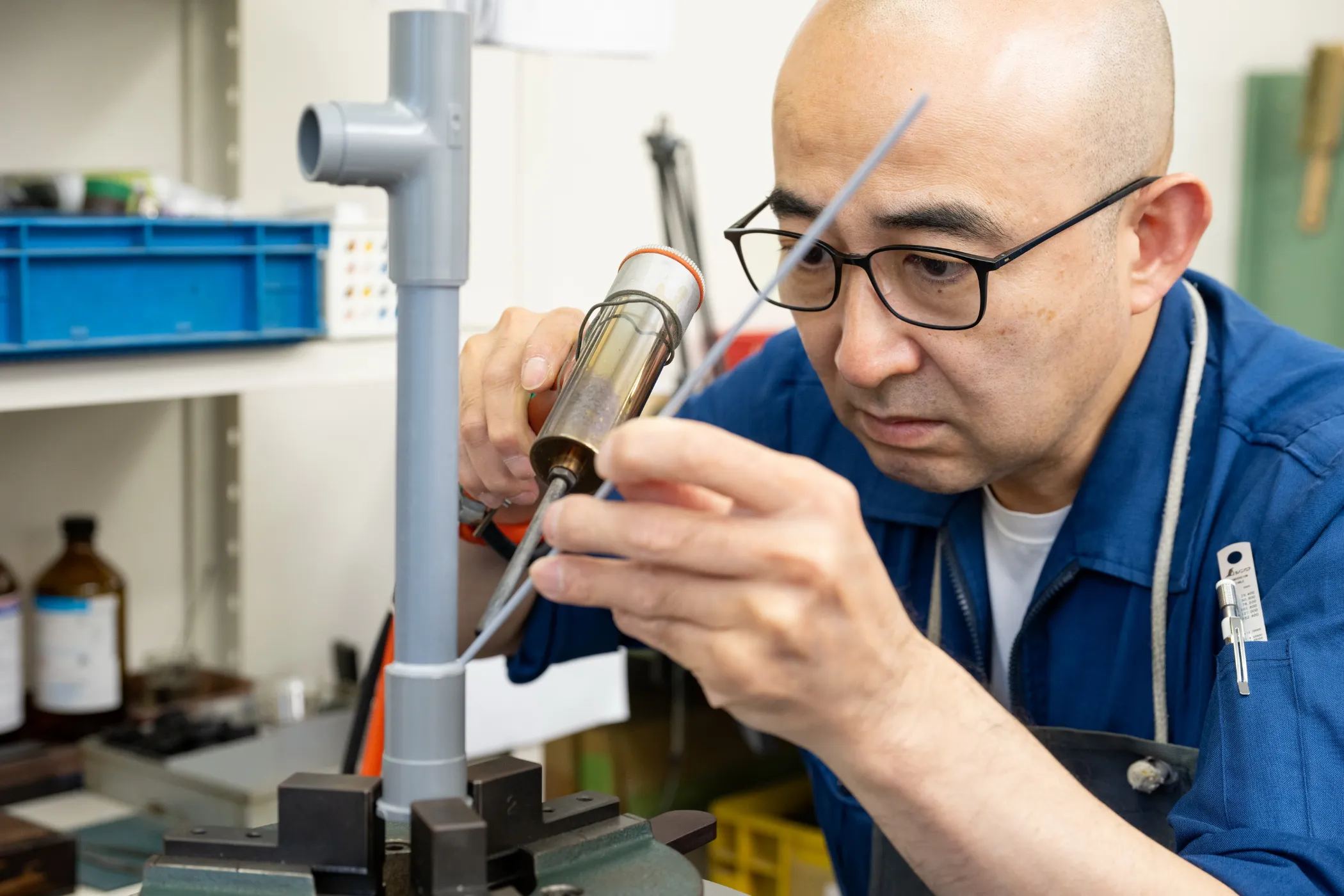
職人の技が光る樹脂溶接
樹脂溶接・曲げ加工を自社工場にて実施
多様な材質での溶接経験があります。
お気軽にご相談ください。
樹脂溶接・溶着の基礎知識
樹脂溶接は、現代の製造業において欠かせない加工技術のひとつです。樹脂溶接の種類は多いため活用範囲が広く、さまざまな部品の接合に使用されています。
樹脂溶接とは
プラスチック製品の開発・生産において、樹脂溶接は重要な役割を担っています。一体成形が難しい構造の部品を作成する場合などに、なくてはならない加工技術です。ここでは、樹脂溶接の特徴とメリット・デメリット、溶着との違いについて解説します。
樹脂溶接の特徴
樹脂溶接は、熱可塑性プラスチックの性質を利用した溶接法です。熱可塑性プラスチックは高温状態で軟化し、さらに温度を上げると溶融します。この性質を利用して、樹脂製の部材や溶接棒を、熱または圧力で溶かして結合する方法です。溶接棒は基本的に溶接したい材質と同じものを使用します。
樹脂溶接には以下のようなメリット・デメリットがあります。
樹脂溶接のメリット
樹脂溶接は部材同士が溶けて一体化する永久的な接合方法であり、安定した結合が期待できます。接合部分の気密性が高く、シール性能を要求する場合にも有効な加工法です。さらに、接着剤やネジなどの消耗品を必要としないため、部品点数の削減やコストの低減にもつながります。樹脂成形や樹脂切削では作成が困難な製品形状でも、樹脂溶接を駆使すれば実現できる場合があります。
樹脂溶接のデメリット
樹脂溶接では熱や圧力を利用するため、部材に歪みが発生するリスクがあります。これは接合部分のみが加熱されることで起こる、不均一な膨張や収縮によるものです。また、一度樹脂溶接をしてしまうと、分解するには物理的な破壊以外の方法がありません。メンテナンスや修理で分解する部品の接合に関しては、樹脂溶接よりもネジ止めなどのほうが適切です。樹脂溶接を手作業でおこなう場合、作業者のスキルによって品質にばらつきが出ることがあります。
溶着との違い
溶着は接合剤を溶かして接合する、もしくは加熱・溶融した部材同士に、圧力を加えて接合する方法です。原理的には樹脂溶接と溶着の間に大きな違いはありません。一般的には接合部分が見えるものを樹脂溶接、見えないものを溶着として区別するケースが多いようです。英語では樹脂溶接も溶着も「welding(resin/plastic welding)」といい、同様の加工法として扱われています。
樹脂溶接の種類
樹脂溶接や溶着には多くの種類があります。
・熱溶接(熱風溶接、熱板溶接、振動溶接、スピン溶接)
・摩擦溶接
・レーザー溶接
・高周波溶接
・超音波溶接
以下、それぞれの溶接/溶着について解説します。
熱風溶接/溶着
熱風溶接は熱溶接のひとつで、部材の溶接面に熱風を吹きつけてプラスチックを溶接する方法です。通常、熱空気や熱不活性ガスによる熱風で、母材と同質の溶接棒を溶かして接合させます。熱風溶接はホットジェット溶接とも呼ばれます。大掛かりな装置や専門的な技術がなくても熱風溶接をおこなえますが、加熱速度が遅いため溶接作業の効率は良くありません。
熱板溶接/溶着
熱板溶接はホットプレート溶接ともいい、高温の熱板を接合部に押し付けてプラスチックを溶接する方法です。大型部材の接合に適した熱溶接で、高強度の溶接継手を作成することができます。一方、薄いプラスチック板の接合には不向きで、熱板溶接機にも定期的なメンテナンスが欠かせません。さらに、熱板溶接は消費電力が大きいうえに悪臭も発生させるため、環境負荷が高いことにも留意しておく必要があります。
振動溶接/溶着
振動溶接は、摩擦熱を利用してプラスチックを接合させる熱溶接です。部材を所定の変位で移動させるリニア振動溶接と、円運動で振動させる軌道振動溶接があります。接触しているプラスチックが、特定の周波数と振幅によって振動して摩擦熱が生じ、部材同士を溶融接合することができます。
振動溶着には消耗材が不要で、表面処理もさほど必要ありません。エネルギー効率が良いうえに、さまざまな形状の樹脂部品を溶接可能です。しかし、溶接面が平坦・水平でなければならないこと、対応素材が限られていること、加工コストが高くなること、などがデメリットとして挙げられます。
スピン溶接/溶着
スピン溶接も熱溶接のひとつで、一方の部品を静止させた状態で、もう一方の部品を回転運動でこすり合わせるか、回転運動を与えた溶接棒を押し付けることによってプラスチックを溶接する方法です。
スピン溶接は比較的シンプルな加工法であるため、高度な専門技術は必要ありません。消耗材を使用せず低コストで、溶接サイクルも早いです。仕上がりも良く、多くの熱可塑性プラスチックに対応できます。ただし、対称な表面のある部品や、円筒形の部品しか溶接できないことに注意が必要です。大型部品の溶接が難しく、部品の位置決めにも技術が求められます。
摩擦溶接/溶着
摩擦溶接は摩擦圧接ともいい、接合するプラスチックを高速で擦り合わせ、発生する摩擦熱を利用して溶接する手法です。摩擦熱によって軟化した母材に、適切な圧力を加え続けることで接合させます。摩擦溶接には「連続誘導摩擦溶接」と「慣性摩擦溶接」の2種類があります。
酸化物や汚染物質を容易に除去でき、異種プラスチックの接合にも対応します。熱による歪みが少なく、高速接合も実現でき、自動制御による無人化も可能です。しかし、摩擦溶接では径が小さい、または非常に大きい母材を接合するのは難しく、接合しようとする母材に適合した圧接機を選択する必要があります。
レーザー溶接/溶着
レーザー溶接は、レーザー光の熱を利用してプラスチックを接合する技術です。「レーザー光を吸収する樹脂」と「レーザー光を吸収しない(透過する)樹脂」を重ね、吸収する樹脂だけを発熱・溶解させて溶接します。接合部分以外が熱の影響を受けにくく、母材が変形することを防ぎます。
レーザー溶接は非接触で接合するため、ワークに摩擦や圧力などによるダメージを与えません。これにより、高精度で美しい仕上がりを実現することができます。一方、透過率が低くなるほどの厚みがあるプラスチックには適用が難しく、気孔ができたり脆性破壊が発生したりする可能性があります。さらに、レーザー溶接に必要な設備投資費用も高額です。
高周波溶接/溶着
高周波溶接では、高周波(13〜100 MHz)の電磁場を利用して、プラスチック内部の分子を高速で振動させます。分子同士の摩擦による熱でプラスチックを溶解し、母材の接合をおこなうという方法です。内部発熱を利用するため外部から熱を供給する必要がなく、母材の特定部分だけを効果的に溶接できるというメリットがあります。
熱影響を狭い範囲に抑えて、非溶接部分への影響を少なくすることができます。有毒ガスや騒音も発生せず、安全性にも優れているのも特長です。デメリットとしては、使用する機械によっては加熱範囲が狭いことや、シート状またはフィルム状の素材しか溶接できないことが挙げられます。
超音波溶接/溶着
超音波溶接は、人間の耳には聞こえない高い周波数(15〜200 kHz)の音、すなわち超音波を利用する溶接法です。超音波の振動を使用してプラスチックなどの材料の内部を発熱させ、素材を溶融させ接合します。原理的には高周波溶接と同じです。
消費電力の低さや溶着サイクルの早さ、仕上がりの美しさなどが特長です。バリの発生を抑えられるため、きれいに仕上げられます。ただし、大型の部材や複雑な形状、三次元形状など、超音波が伝わりづらい場合には不向きです。
樹脂溶接部品の用途
樹脂溶接部品は、以下のような用途で活用されています。
航空・宇宙
機体の内装パネル、保持タンク、トレイなど。
自動車
フロントグリル、ラジエーター、バッテリーケース、ホイールウェルライナー、バンパーなどの樹脂部品。
船舶
ボートやバラストタンク、魚の飼育井戸、貯水タンクなど。
農業
ガスケットやPVCフェンス、タンク、給水・ミストラインなどの樹脂部品。
配管
DWVパイプや排水管、蛇口など。